If stores want to do well in today’s fast-paced world, they need to make them work better. The ability to keep and find things better is no longer a nice-to-have; it’s a must because prices are going up and competition is tough.
A lot of good things happen when you store and move goods through your warehouse efficiently:
- Lowering the amount of room needed for storage, making it easier to find products, and streamlining workflows all save a lot of money.
- Better customer satisfaction: Customers are happy when their orders are filled faster and delivered more quickly.
- Better inventory management: Being able to see real-time stock levels and making good use of room help avoid running out of stock or having too much of it.
But how do you get to this dream warehouse? According to Speedrack West push back racks are a new way to store things that is becoming popular.
What push back racks are and how they work
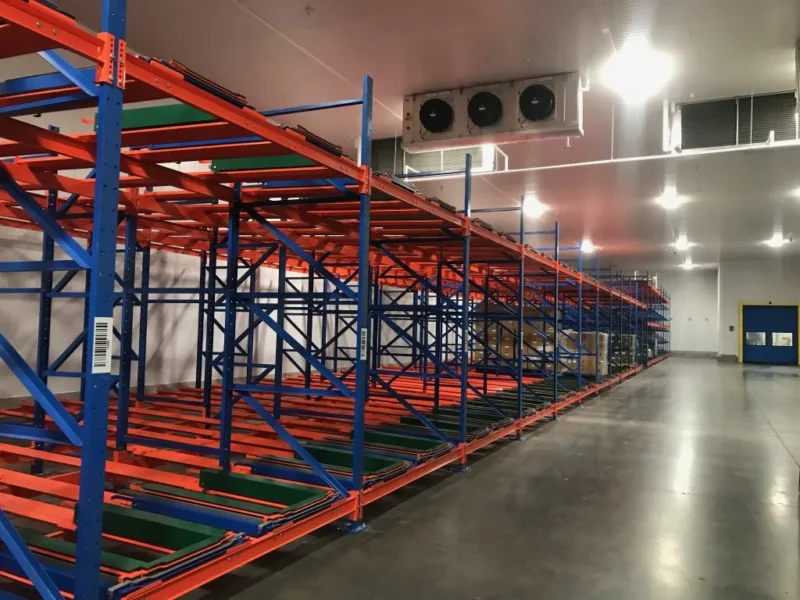
Push back racking is a high-density storage system that makes the best use of room while still making it easy to get to each pallet. Think of a system that is a mix of selective racking and drive-in racking. Like selective racking, boxes are put on and taken off of a single aisle. In push back shelving, however, wheeled carts that roll on inclined tracks are used instead of just one pallet per level. You can put two to six boxes on these carts at a time, one behind the other.
Here’s how it works:
- Loading: A forklift places a pallet on the top cart.
- Pushing Back: As subsequent pallets are loaded, the first pallet gets pushed back, exposing the empty cart underneath.
- First-In, Last-Out (FIFO) Flow: When unloading, the forklift retrieves the pallet at the front. This causes the remaining pallets to be pushed forward, maintaining an easy access to the next pallet.
This “push back” process efficiently utilizes space within the system, allowing you to store significantly more pallets compared to traditional racking solutions.
Benefits of Push Back Racking
So, how does push back racking contribute to maximizing warehouse efficiency? Let’s explore some key benefits:
1. Unleashing Space Magic: Maximize Your Cube with Push Back:
Imagine squeezing 70% more storage into your existing warehouse footprint. Imagine getting 70% more storage space into the space you already have for your business. Push back racking has the power to change things like that. In standard selective shelving, each bay can only hold one pallet. But with push back systems, you can stack pallets two to six deep in each lane by using wheeled carts on slanted rails.This smart way to make the most of space frees up useful square footage. This could let you shrink your building or use the extra room for useful tasks like processing or packaging.
2. Ditch the Maze, Embrace the Streamline: Unleash Operational Efficiencies:
Drive-in racking systems may boast high density, but navigating their labyrinthine aisles with forklifts can be a slow and error-prone dance. Enter push back racking, the champion of streamlined workflows. Because it only has one aisle, workers don’t have to do any forklift gymnastics. They can just drive straight down the lane, pick up their pallet, and be on their way. This means that orders will be picked up faster, customers will be happy while they wait for their deliveries, and picking times will be shorter.
3. Cost Savings Symphony: A Harmonious Blend of Efficiency and Optimization:
Push back racking’s efficiency concerto delivers a beautiful symphony of cost savings. The increased storage density reduces your rental overhead by maximizing the value you squeeze out of every square foot. Faster picking translates to lower labor costs, as operators whiz through their tasks. You also save money on lighting, heating, and repairs because you don’t have to build any more lanes. As a result? A harmonious choir of lower costs that makes your bottom line sweeter.
4. Inventory Management Made Easy: FIFO Flow Takes the Reigns:
Push back racking adheres to the Last-In-First-Out (LIFO) inventory management principle, where the most recently loaded pallets are retrieved first. This keeps older stock from sitting on the shelves for too long, which lowers the chance that it will go bad or become outdated. Also, the system’s easy access and clear view make real-time inventory tracking a breeze, which helps you avoid expensive stock-outs and overstocks.
5. Beyond the Numbers: Safety, Adaptability, and Scalability:
It’s not just for numbers that push back racking is good for. Truck traffic is cut down by the warehouse’s single aisle, which makes it a better place for everyone to work. The system can easily be changed to fit changing storage needs because it is made up of separate modules. It can also handle boxes of different sizes and weights. As your business grows, it’s also easy to add on to push back shelves to meet your new storage needs. To put it another way, it’s an investment that will last. With push back racking, we can do more than just fit more pallets into a spot. We can also save money, be flexible, and make the most of the room we have. Give push back racking a standing ovation if you want to run your business more quickly and effectively.
Conclusion
Putting in place push back racks needs careful planning and execution. Things like pallet weight, product turnover, and the way things are run are important to keep in mind if you want to be successful. The change can go more quickly and easily if you work with skilled professionals. It’s easier to run a building when the shelves are pushed back. Businesses that want to streamline their logistics will find its high-density storage, faster picking times, and lower running costs very appealing. To find out if push back racking is right for your warehouse, carefully look at your needs and the way your product is stored. Your business will run more smoothly and have an edge over its rivals if you use this new way to store things.